The Early Days and Delta Elevator’s First Machine
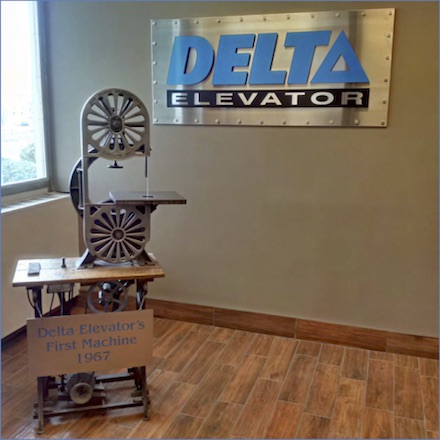
Here is the story behind that one-of-a-kind contraption.
In July 1967, things looked bleak at Delta Elevator. Barely three month old, the company had earned a total of $300 in revenue. Not enough to make a living for its founder, Water Guderian.
But as happens in life, opportunities arise that can set the future course of an organization if seized at just the right moment. For Delta, that opportunity was the issuing of the “Bells and Whistles” directive in the summer of 1967.
This directive, known as Section 22, required all elevators in Ontario to be retrofitted with a constant pressure stop switch, a bell indicating when the inner door was open between floors, and an extended toe guard.
The University of Guelph was one of the first to respond to the directive and issued a public tender for the retrofit of its elevators. Delta Elevator submitted a competitive bid... a bid so competitive that they were given an opportunity to withdraw it because “it must contain an error it was so low”!
Nevertheless, Walter took on the work, figured out how to make the project profitable, and became somewhat of an expert at Section 22 retrofits in the Kitchener-Waterloo area. Delta Elevator eventually secured the contracts to do the work for Wilfrid Laurier University, University of Waterloo, and Mutual Life Insurance.
The rest, as they say, is history.
What many people are not aware of is the role Delta Elevator's first machine played in this work. The toe guard extension required quite a bit of metal work and cutting. Doing this by hand was a time consuming task, so Walter set about to find a better alternative. A standard band saw for steel was much too expensive at that time in the company's history, so the solution would have to be something less cash-consuming.
A trip to the local auction house provided the raw material: An old foot-powered Singer sewing machine and a band saw meant for wood.
Through the hallmark ingenuity that defines Walter, the two were married together to become Delta Elevator's first piece of machinery. The key to the undertaking was figuring out how to slow the high speed of the band saw (which is needed for working with wood) to the appropriate speed for working with steel. This was accomplished through a series of pulleys and belts, which are still visible under the sewing machine platform.
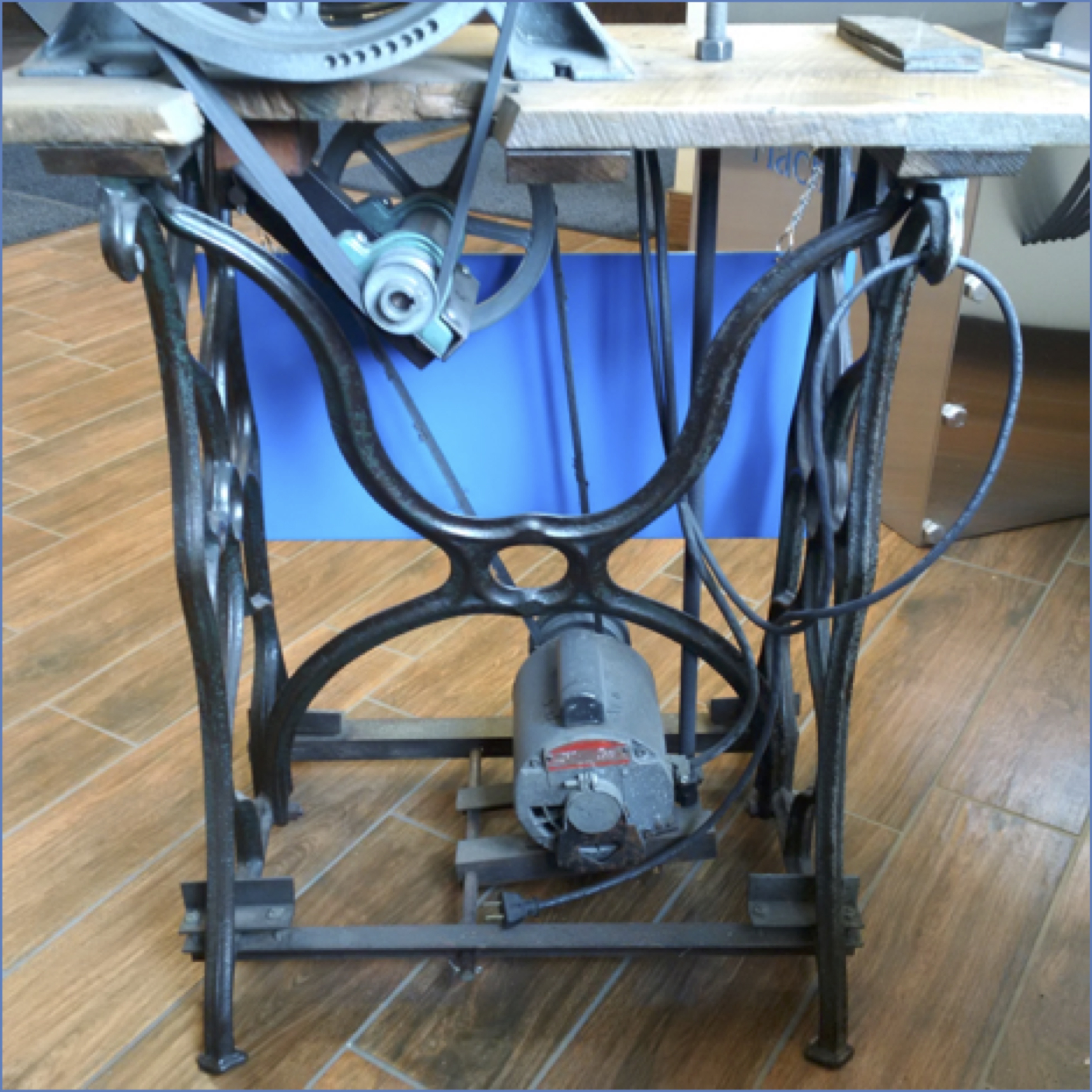
Today, Delta Elevator's Manufacturing Department enjoys the benefits of machines like CNC press brakes and laser cutting equipment, which provide much better accuracy and repeatability.
But that hybrid sewing machine / band saw served the company well in those early days, and helped set Delta Elevator on the path to long term success.